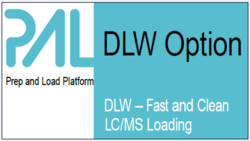
Introduction of the Dynamic Load and Wash (DLW) option represents a new concept in wash station for the CTC PAL. DLW combines injection and wash steps while minimizing wash time and carryover.
Wash solutions are actively pumped through the DLW by two self priming micro pumps. DLW pumps are sensitive to particulates introduced by wash media and back pressure from blockages. Operating the system with a blockage or compromised component can damage the DLW. Recognizing and promptly correcting DLW problems is extremely important. Please see DLW: Diagnosis and Troubleshooting Guide and DLW: Best Practices for assistance.
As of Jan 2017, CTC Analytics, the manufacturer of the PAL and the DLW option, recommends protecting each DLW micro pump with a check valve on the outbound fluid side. Autosampler Guys offers this part as: PAL DLWCHKVLV $146 per valve – two are required.
DLW: Diagnosis and Troubleshooting Guide
Known reported symptoms with related cause:
- One reservoir fluid level is dropping but other is rising” – usually Wash 2.
This is caused by a ruptured valve diaphragm on the impacted side. Wash fluid if being forced backwards through the inactive pump and into the connected reservoir. Pump must be replaced. DLW ACT valve might also be involved if no flow from needle tip when working pump is running.
- No blue LED illuminated when the DLW is operating. No flow from the needle tip.
Caused by an electrical problem either in the injection head or DLW PCB. The difference can’t be determined by the user. Please contact us for options.
Troubleshooting Steps:
- Confirm presence of wash solution in each reservoir and that the inlet filter on each solvent line is present and fully immersed.
- Visually check that tubes between the reservoir bottles and the DLW micro pumps are fully primed.
- Test each DLW micro pump with the CTC Pal handheld terminal:
- Press the F1 Menu Key
- Select Utilities
- Select Wash Stations
- Select Wash 1
- Manually lift the lower needle guide to expose the needle tip and place a reservoir under the needle tip to catch wash solution. Press the F2 “ACT” to activate the pump.
- Does the blue LED illuminate on the DLW adapter seen through the transparent cover over the injection head syringe area? If not, there is an electrical problem. Please contact us.
- Do you see a consistent, fast stream of fluid exiting the needle tip? If not, immediately press the F2 DEACT key on the PAL control terminal to stop the pump. (Flow from needle tip that is less than expected, inconsistent or absent can be due to a blockage in the needle. If you have a DLW-1 with separate needle and TEF holding loop, try replacing the needle and repeating item 3 steps a-e. If you have a DLW-2 with one-piece stainless steel needle and loop assembly, proceed with steps Item 3 steps f and g and then move on to Item 4.)
- Press the F2 DEACT key on the PAL control terminal to deactivate the pump.
- Repeat the test process for Wash 2.
- If either or both pumps are failing to produce the expected flow at needle tip and replacement of DLW-1 needle fails to correct, it is necessary to test the pumps while disconnected from the DLW manifold. Follow these steps:
- Disconnect the liquid transfer line that connects Wash 1 micropump to the top port on the DLW manifold. You will find this line connected to the protrusion from the slot on the left side of the PAL injection head.
- Place the disconnected line in a collection reservoir and activate Wash 1 as you did above in Item 3. Expect a fast, solid stream of wash solution. If this is present, deactivate the pump and reconnect the open line to correct DLW manifold port.
- Repeat for Wash 2.
- If flow is lower than expected or absent, a bad pump is suggested. Pumps can fail alone or in pairs.
- If either or both pumps are failing to produce the expected flow at needle tip and replacement of DLW-1 needle fails to correct, it is necessary to test the pumps while disconnected from the DLW manifold. Follow these steps:
- Select a Syringe Wash by following this path on the PAL control terminal “Home/Menu/F2 Syringe Wash”.
- While wash proceeds, observe the syringe barrel for bubbles and incomplete filling during the plunger upstoke. If observed and you haven’t replaced the DLW-1 needle or DLW-2 needle/loop assembly, proceed with replacing at this time.
- If there are still bubbles and/or incomplete filling of syringe during wash after needle replacement, it would indicate the DLW actuation valve isn’t working. The DLW actuation valves fails in closed position creating a complete or almost complete blockage. The next step would be to replace the DLW actuation valve.
- If both pumps are operating normally and 1) you are getting normal flow with transfer lines disconnected 2) blue LED illuminates when pump is activated 3) there is still little or no flow at needle tip:
DLW: Best Practices
- Ensure wash solutions are particle and fiber free.
- Outfit both pumps with a PAL.DLWCHKVLV on the outbound fluid side.
- Change the valve inlet needle seal regularly.
- Properly teach the DLW needle position at the injection inlet. This position is different from the legacy, non-DLW needle position. Improperly teaching this position will negatively impact DLW wash performance.
- Ensure reservoir filters provided with the DLW option kit are still fitted and intact. If not, please replace.
- Regularly confirm that you see the blue LED illuminate when the DLW is washing.
- Check DLW syringe for wear. Some visual indications are bubbles forming in the barrel during washing and liquid leaking up the bore of the syringe and escaping from the top. Removing the syringe and manually moving the plunger will confirm if replacement is necessary. Remember to loosen and tighten the syringe at the DLW manifold using the knurled ring at the bottom of the barrel and not by turning the barrel.
- Stock spare DLW-1 needles or DLW-2 needle/loop assembly.
- Consider stocking a spare DLW pump.